The use of calcium carbonate (PCC) in polymers has a long history. The use of calcium carbonate (PCC), in addition to the decrease in final product cost and the reduction of polymer consumption, also contributes to the mechanical strength and physical and appearance properties of the product. The use of Precipitated calcium carbonate (PCC) due to its high purity results in the reduction and elimination of undesirable effects, including corrosion of the cylinder and the screw and the wear of the devices, and, on the other hand, due to uniformity of distribution and non-isotropic shape results in increased mechanical strength.
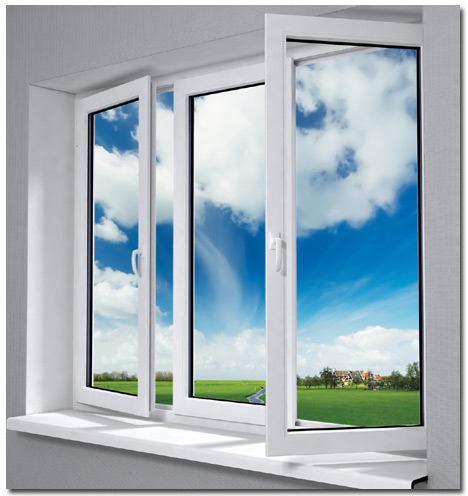
Application of PCC in PVC industries
The use of Precipitated calcium carbonate
, The use of Precipitated calcium carbonate (PCC) is an effective way to solve the problem of low gloss of profiles and other products made from PVC. In this way replacing Precipitated calcium carbonate (PCC) instead of natural calcium carbonate (GCC) can simultaneously act as a processing aid and increase the impact resistance gloss of the product.
PVC-based component
The use of PCC in the production of PVC-based components, especially UPVC, is very important, So that very fine PCC particles can facilitate PVC processability and result in special improvements in its major properties such as impact resistance, surface properties and dimensional stability. In this way, by increasing the speed of production and also as an agent for controlling the rheology and process, also reduces the need for other additive in the formulation. The chemical modification of the surface of PCC leads to good interaction of this material with PVC, and its mechanical properties and its tensile strength become better than the ground calcium carbonate (GCC, in a variety of PVC-based products, Including UPVC door and window profiles, various types of pipes and fittings, cable lining and cable granules, types of flooring, wall coverings and floating sheets, artificial leather and industrial plastics.